What companies get wrong about safety investments
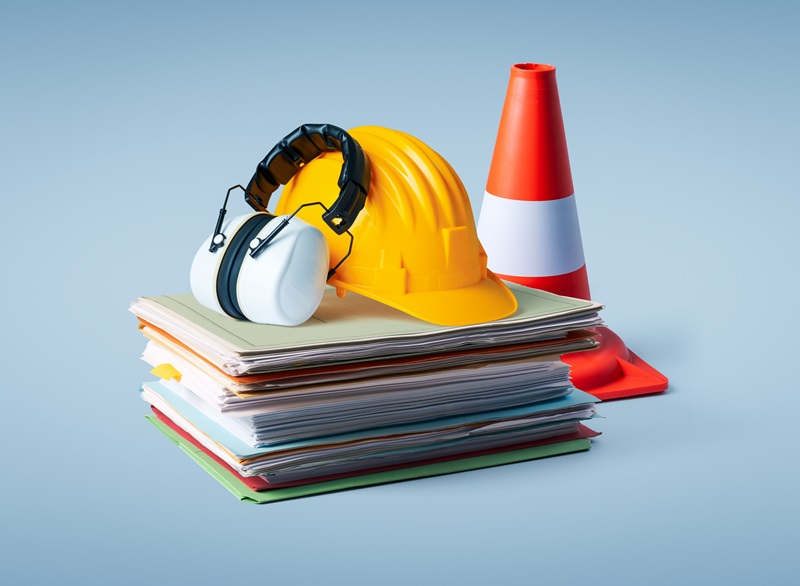
Companies have devoted considerable resources to reducing injuries and conditions have improved, but not enough. Employers reported 2.8 million injury and illness cases in 2022, a 7.5 percent increase over 2021. There were 5,486 fatal work injuries in 2022—the equivalent of one death every 96 minutes. Here are seven reasons why more effective injury and fatality reduction is elusive.
- Companies see safety as a cost rather than a performance driver
According to a recent report in the Harvard Business Review most executives see safety as a “cost to be incurred today to mitigate losses tomorrow” rather than a performance driver. There’s a heavy emphasis on compliance and reacting to problems, rather than viewing safety as a strategic driver of customer satisfaction, sales, margins, contract opportunities, efficiency, employee retention and recruitment, reputation, lower claim costs, and reduced litigation. Consequently, safety investments considered loss avoidance rather than profit boosters attract fewer dollars and companies underinvest.
The report cites several empirical examples demonstrating that safety investments increase customer satisfaction, employee morale, sales, margins, pricing power, market share, and long-term firm value and reduce healthcare and litigation costs. One such study, a 19-year panel study of 619 publicly traded companies, revealed that firms with better employee safety records enjoyed significantly higher customer satisfaction than companies with lower safety records. Customer satisfaction is strongly associated with sales growth, bigger margins, and superior shareholder returns.
- Safety is treated as a stand-alone initiative
Another thing companies get wrong about safety is treating it as a stand-alone initiative, separate from the core business strategy. Treated as a set of rules or tactics, employees view it as an additional burden and employers put it on the back burner when it’s working well or cut costs when under financial pressure. Such an approach fuels the conflict of productivity vs. safety and promotes silos. While safety is established as an expectation, it lacks integration into operational decisions and doesn’t work effectively towards the main goal of business success.
- Specific safety targets aren’t defined
While broad objectives such as achieving zero injuries are important and establish foundational goals, without a plan to identify and address top exposure risks, the goal can seem out of reach and meaningless to employees. Safety targets should be specific, measurable, and achievable within a specified time frame and designed to address the top risks in your company. Some examples are increasing employee involvement in hazard identification, encouraging near- miss reporting, reducing the number of slip and fall injuries, improving ergonomic safety training, lowering the number of vehicle-related accidents, and so on.
Some employers, particularly those in high-risk industries with high accident rates, are changing course to focus on life-threatening or life-altering injuries while still recognizing the importance of the Total Recordable Injury Rate (TRIR). For example, Helmerich & Payne, Inc. (H&P), a drilling contractor, adopted an approach that focused on providing a proportionate response to serious incidents such as an employee struck by a dropped drill collar rather than a sprained ankle, to ensure that resources were allocated to removing and controlling serious exposures. It didn’t rely on creating new rules or stronger enforcement of existing ones but led differently by emphasizing potential SIFs and precursors and engaging the workforce for a culture shift. As a result, they have seen a significant reduction in fatal events.
- Too many metrics prevent effective evaluation
Metrics are key to proving that investments deliver fewer accidents, enhanced productivity, and profitability. Yet, many companies have too many generic metrics not clearly linked to safety objectives and outcomes. Too many metrics mean that safety is not effectively measured.
A large facilities management company visited 200 client sites to uncover the drivers of customer value. From the visits, the company defined safety as safe operations by employees (preventing lacerations from sharp tools such as kitchen knives and garden tools) and safe driving (no incidents of drunk driving or speeding infractions). It introduced several new practices to improve safety, replaced older equipment, and equipped vehicles with breathalyzer ignition locks and remote camera monitors to prevent drunk or unsafe driving.
Reducing the number of safety metrics by 50 percent and investing in new technology that shortens the time it takes to gather metrics, enabled the company to effectively measure the results. Equipment-related lacerations dropped by more than 70 percent and vehicular accidents by more than 90 percent. Simplifying the measurement system and ensuring that the metrics align with the specific safety objectives helps build the business case for further investments.
- Generic training fails to improve safety
The Harvard report notes generic training that focuses on communicating the value of safety in the workplace is generally not closely tied to improvements in safety. “Rather, companies should mandate training in behaviors that have been statistically shown to improve safety outcomes.” It gives the example of Dräger, a provider of fixed and portable gas-detection systems for preventing accidents in the oil, gas, and chemical industries. In addition to covering the technical aspects of operating the equipment, the company also emphasizes how to interpret data and explains the response strategies for various scenarios of gas exposure.
Similarly, if employers incentivize safety, they should focus on preventive behaviors and not outcomes. To encourage the use of PPE, a commercial construction firm entered employees who consistently wore all required PPE (helmets, glasses, harnesses) into a monthly drawing for $200 gift cards. Participation was tracked through a smartphone app and within six months PPE compliance had risen from 43 percent to more than 92 percent.
- All aspects of the proposed investment aren’t weighed
Today, more than ever, safety is not static but constantly evolves with changing work hazards and new technologies and processes. This poses significant challenges for employers and wrong decisions can be costly. A National Safety Council’s (NSC) Work to Zero report, Build the Business Case for Safety Innovation, notes although identifying technologies that suit an organization is vital, it isn’t the only aspect that should be considered when developing the business case for safety innovation. “Senior leaders must determine whether technological adoption can occur seamlessly without adversely impacting operational activities, such as job hazard analysis and document control processes. Additionally, as infrastructure, processes, and people represent the business’ fundamental components for operational capacity – the digital readiness of these elements must be critically analyzed, ensuring operational components can actively adapt to technology implementation.”
- There isn’t an ROI analysis
One of the major barriers to implementing safety improvements, such as new technologies or new equipment, is cost. The executive suite wants to know how much of a return it can expect and how long it will take. The NSC offers a return-on-investment (ROI) calculator that allows a company to compare the costs of “business-as-usual” and an investment in eight different key safety technologies. To illustrate, the report compared the ROI of an investment in Proximity Monitoring Wearables designed to reduce transportation or contact-related incidents between employees and machinery/equipment at a large construction company and a small retail business.
While ROI can provide a financial value, it should not be used alone. Coupling this information with the harder-to-quantify factors of customer satisfaction, increased profitability, contract opportunities, efficiency, employee retention and recruitment, and enhanced reputation will elevate safety as a competitive advantage.
SEVEN SECRETS
You’ll receive important information to help you avoid overcharges on your workers’ compensation.